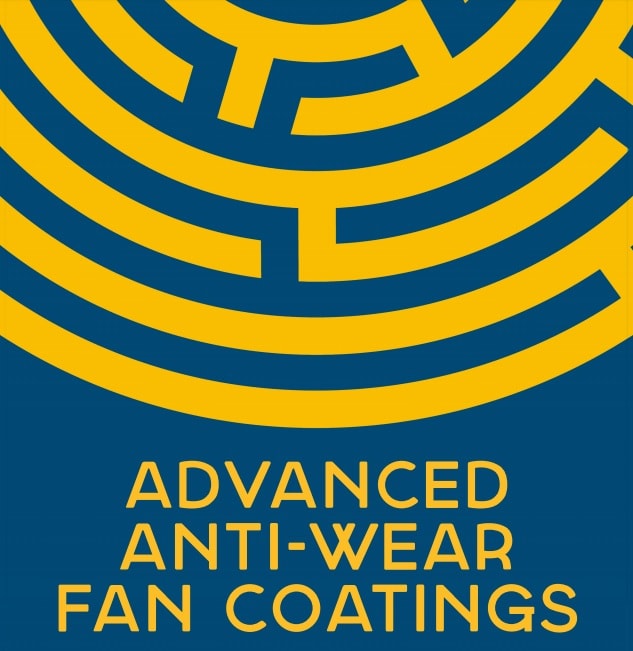
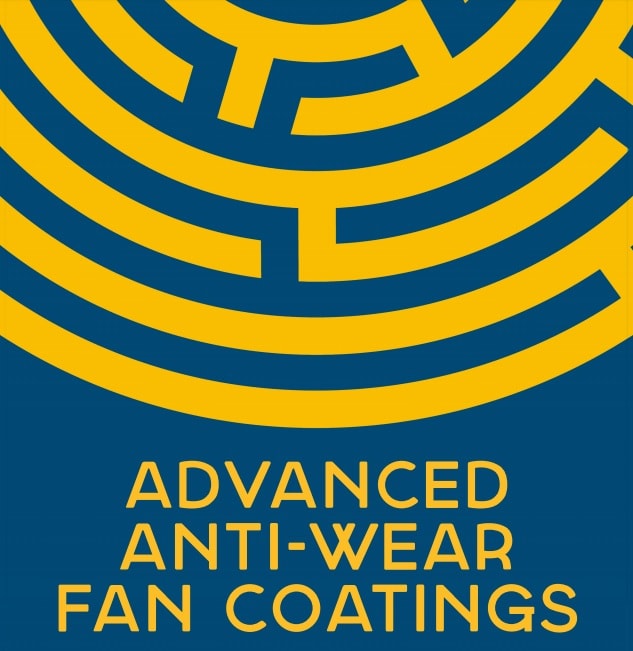
Search
Categories
Recent Posts
-
TLT-Turbo Africa to exhibit Redefined Mine
September 5, 2022 -
TLT-Turbo Africa Continues to Show Resilience
July 7, 2020 -
TLT-Turbo Africa Response to the Coronavirus
March 26, 2020